
Masion D'Être
ABOUT
A Contemporary Fashion House:
Maison D’Être is a sustainable fashion innovation lab and is the brainchild of multidisciplinary designer, Drew Rosen. Every product is sourced from pre-owned material and individually designed around elevating a garment’s history and natural patina, much like the Japanese art of Kintsukuroi, or ‘golden repair.’
Since it’s inception in 2018, Maison D’Être has released several capsules of clothing and jewelry, walked on the runway, and has displayed in several shows. Between countless photoshoots, Maison D’Être has helped companies evaluate methods for managing waste and overstock, worked with clients and friends to bring new concepts to life, and networked with other sustainable designers to learn new methods of sustainability and evolve away from exploitative manufacturing processes.
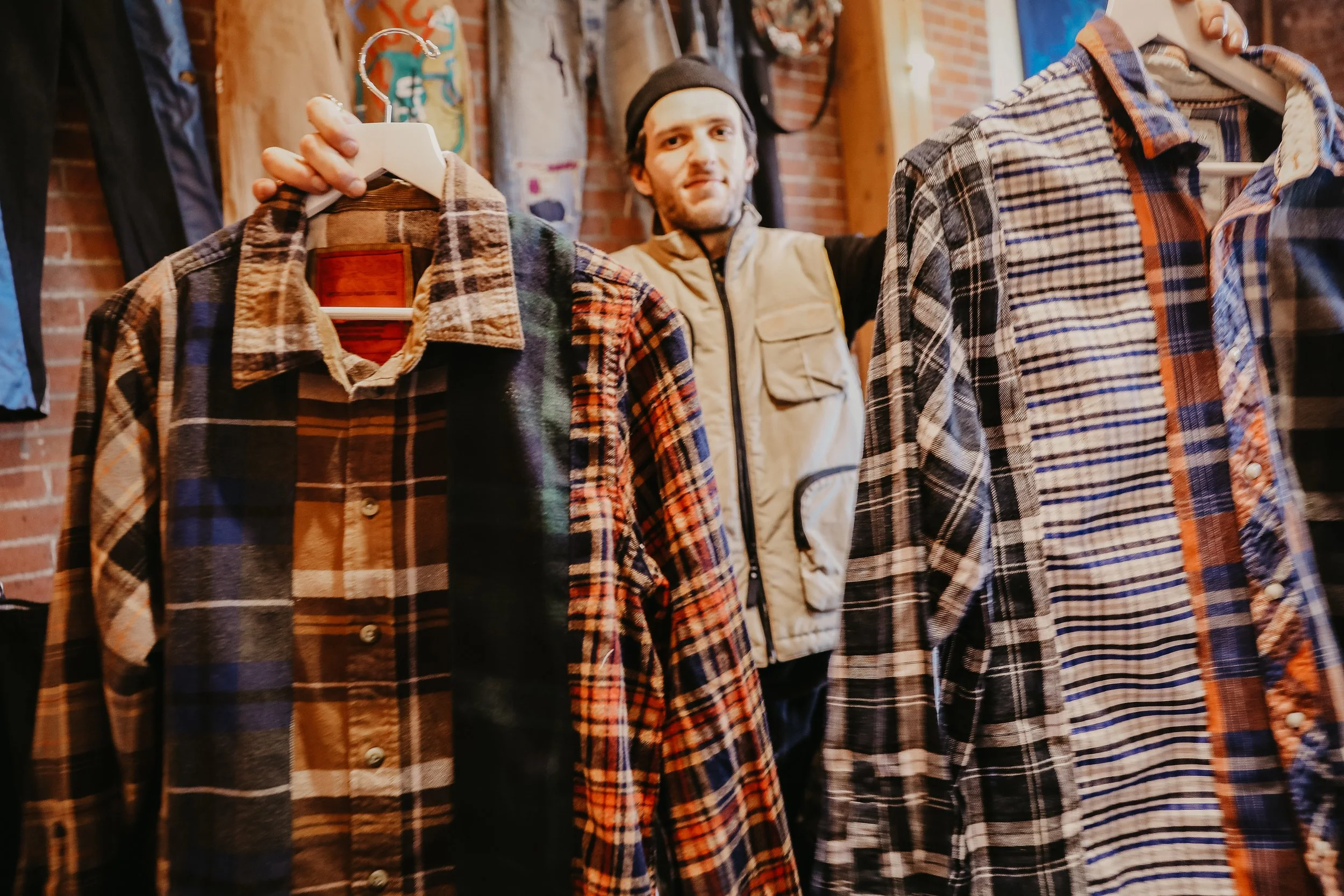
BESPOKE DESIGN FOR CLIENTS
Custom 1 of 1 Pieces for Special Clients
Maison D’Être has always championed creating unique pieces expressly designed for their intended owners. Here are a handful of bespoke designs built intentionally around upcycling a client’s existing clothes and achieving a specific aesthetic.

1 OF 1 CREATIONS
From Thrift Find to Treasure
The origins of Maison D’Être began with combining and tailoring thrifted clothes during my final semester of college. I wanted to create things that felt highly unique and bespoke out of pre-existing clothes and celebrate the existing labor and craftsmanship by incorporating it in a new way into my designs. Here are a collection of unique pieces I was inspired to make from thrift finds.
MICRO-BATCH PRODUCTION
Mélange Denim & Production
With my initial forays into patchwork denim, I would work with scraps and complete pants and often times my scraps would influence my pattern ideas. As I began to refine the production strategy, I began to use patterns. To ensure that every custom made piece was one of a kind and to ensure that as much of the pre-owned denim was used up as possible, I created a three-step process for creating my panels while minimizing on wasted material. Firstly, I dismantled the upcycled denim and salvaged time-intensive parts like waistbands and zippers to be re-used. Next, I cut as many full panel pieces from the material as possible. Once I had cut my pattern pieces and all that remained were my scraps, I would begin to combine scrap pieces until I had enough material to trace another full panel. I would repeat this method until the scraps were too small to sew together. With this method, I created a range of panel styles from solid material to intricate patchwork panels. These panel pieces were then combined to create an even larger and more complex patchwork garments. My first attempt at creating a more streamlined production line was inspired by a conversation with a retired sewing professional. Not only did I save compounded time by doing all of the same types of stitches at once on one machine and then the other, but it gave me the opportunity to chain my stitching which saved me a lot of thread and subsequently time and money.
Mondrian Denim Series 2
Blue Mélange Denim, a series of 6 pairs of patchwork bluejeans - comprised of blue denim material which had been damaged and repaired, or dirtied and needed to be-deep cleaned and used inside out. Process & On-Body & Branding
‘Le Chat Noir’ Denim Collection
Le Chat Noir is the third and most efficient production series of The Mélange and Mondrian Denim production Series. Employing shades of black and grey denim, as well as some additional black material, this series was designed to appeal to designers and F.O.H. staff that I met while living in Providence, RI. Production BTS
DESIGN ARCHIVE & PROCESS
A Look Behind the Curtain
Over the past five plus years of designing I have made a lot of garments and learned from practice and from failure. Enjoy some of my earlier projects and a bit of the process involved with realizing them.